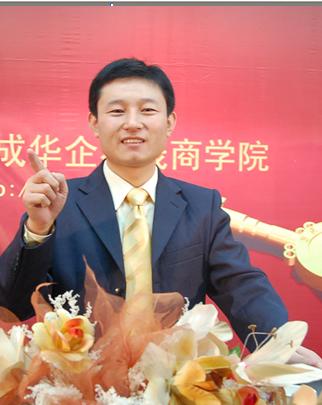
張小強(qiáng) 教授
- 關(guān)注者:人 收藏?cái)?shù):人
- 所在地區(qū): 廣東 深圳
- 主打行業(yè): 不限行業(yè)
- 擅長(zhǎng)領(lǐng)域:生產(chǎn)采購(gòu)生產(chǎn)管理
- 企業(yè)培訓(xùn)請(qǐng)聯(lián)系董老師
- 聯(lián)系手機(jī):

張小強(qiáng)老師培訓(xùn)聯(lián)系微信

掃一掃,關(guān)注公眾號(hào)

張小強(qiáng)老師的內(nèi)訓(xùn)課程
前言:1. 質(zhì)量經(jīng)理人及質(zhì)量工程師的角色認(rèn)知2. 質(zhì)量經(jīng)理人及質(zhì)量工程師的能力素質(zhì)模型影片:質(zhì)量意識(shí)一、質(zhì)量管理的三個(gè)歷史衍變階段1. 質(zhì)量檢驗(yàn)階段QC 2. 統(tǒng)計(jì)質(zhì)量控制階段SQM 3. 全面質(zhì)量管理階段TQM 二.全面質(zhì)量管理的四個(gè)基本要求 1. 全員參與 2. 全過(guò)程的質(zhì)量管理3. 全組織的質(zhì)量管理4. 多方法的質(zhì)量管理三、TQM質(zhì)量管理八大原則1. 以客戶為關(guān)注焦點(diǎn)2. 領(lǐng)導(dǎo)作用3. 全員參與4. 過(guò)程方法5. 管理的系統(tǒng)方法6. 基于事實(shí)的決策方法7. 持續(xù)改進(jìn)8. 與供方互利關(guān)系四、TQM全員面質(zhì)量管理系統(tǒng)構(gòu)建1. 企業(yè)品質(zhì)職能機(jī)制2. ISO91品質(zhì)管理系統(tǒng)3. QC8環(huán)保管理系
張小強(qiáng)查看詳情
部分:生產(chǎn)瓶頸的表現(xiàn)形式 1. 工序方面 2. 半成品方面3. 均衡生產(chǎn)方面 4. 生產(chǎn)線方面第二部分:引發(fā)生產(chǎn)瓶頸的因素 1. 材料因素 2. 品質(zhì)因素 3. 工藝因素4. 人員因素 5. 突發(fā)性因素 6. 時(shí)間因素第三部分:生產(chǎn)瓶頸解決之道 一、透過(guò)品質(zhì)預(yù)防解決生產(chǎn)瓶勁1. 品質(zhì)預(yù)防的五大要素2. 品質(zhì)預(yù)防四大成本透視3. 生產(chǎn)現(xiàn)場(chǎng)品質(zhì)預(yù)防六大方法4. 品質(zhì)檢驗(yàn)勝于品質(zhì)預(yù)防二、透過(guò)流程再造解決生產(chǎn)瓶勁1. 流程再造四步法2. 實(shí)戰(zhàn)訓(xùn)練:切銅管流程改造3. 妥善排班的方法4. 實(shí)戰(zhàn)訓(xùn)練:電器生產(chǎn)線人員排班5. 如何進(jìn)行作業(yè)切換6. 實(shí)現(xiàn)“零”切換的思路三、透過(guò)
張小強(qiáng)查看詳情
章:企業(yè)生產(chǎn)中常見(jiàn)的問(wèn)題 1. 管理者真正的價(jià)值2. 生產(chǎn)現(xiàn)場(chǎng)常見(jiàn)的問(wèn)題及錯(cuò)誤的解決方法3. 探尋生產(chǎn)問(wèn)題的產(chǎn)生源頭第二章:全面分析生產(chǎn)問(wèn)題的關(guān)鍵 1. 企業(yè)組織架構(gòu)與組織運(yùn)作產(chǎn)生沖突的原因2. 解決組織運(yùn)作中的沖突:流程改造與組織重組3. 企業(yè)問(wèn)題的演變和確保流程有效的標(biāo)準(zhǔn)化技巧第三章:解決生產(chǎn)問(wèn)題的基礎(chǔ) 1. 流程改造的切入點(diǎn)2. 流程改造的步驟第四章:發(fā)現(xiàn)問(wèn)題的工具 1. 異常處理的步:發(fā)現(xiàn)異常2. 5S實(shí)務(wù)的應(yīng)用第五章:記錄與歸納問(wèn)題的法寶 1. 3UMEMO(改善備忘錄)2. 觀察3UMEMO的技巧3. 改善備忘錄的應(yīng)用及范例第六章:分析問(wèn)題的方法 1. QC七大手法2. PDCA手
張小強(qiáng)查看詳情
一、錯(cuò)誤產(chǎn)生的原因 1、不小心2、環(huán)境惡劣3、不習(xí)慣4、誤會(huì)二、防止錯(cuò)誤的手段 1、防止錯(cuò)誤的手段2、接觸式探測(cè)3、定數(shù)式探測(cè)4、標(biāo)準(zhǔn)動(dòng)作異常探測(cè)三、處理異常停止的對(duì)策 1、處理異常停止的對(duì)策2、異常停止的特點(diǎn)3、查找異常停止的原因和處理異常停止的對(duì)策4、把握發(fā)生地點(diǎn)5、仔細(xì)分析作業(yè)6、清掃設(shè)備和地板7、查找輕微缺陷8、重新確認(rèn)運(yùn)轉(zhuǎn)條件9、制定作業(yè)標(biāo)準(zhǔn)書四、寫給不能發(fā)現(xiàn)改善主題的人 1、把危機(jī)感一代一代地傳遞下去2、如何明白浪費(fèi)3、明確目的4、排除過(guò)于膨脹的工作5、把企業(yè)當(dāng)成家庭一樣來(lái)考慮、行動(dòng)6、細(xì)心地分析現(xiàn)狀,就能找出原因7、學(xué)會(huì)解決問(wèn)題的手法8、寫給不能發(fā)現(xiàn)改善主題的人...
張小強(qiáng)查看詳情
一、 制造企業(yè)現(xiàn)場(chǎng)管理的六個(gè)終極目標(biāo) 品質(zhì) 效率 成本 交期 安全 士氣二、 造企業(yè)現(xiàn)場(chǎng)管理的五個(gè)核心要素 人員 設(shè)備 材料 方法 環(huán)境三、 生產(chǎn)現(xiàn)場(chǎng)效率低下的十個(gè)拐點(diǎn) 1. 人工成本與生產(chǎn)效率不成正比2. 設(shè)備損失及稼動(dòng)率低下3. 物料延期及周轉(zhuǎn)期長(zhǎng)4. 臨時(shí)插單與急單的影響5. 沒(méi)有找到有效的改善方法6. 未使用IE技術(shù)進(jìn)行改善7. 生產(chǎn)現(xiàn)場(chǎng)職能化8. 沒(méi)有目視管理或沒(méi)有提取生產(chǎn)關(guān)鍵指標(biāo)9. 沒(méi)有有效的生產(chǎn)效率考核體系10. 生產(chǎn)現(xiàn)場(chǎng)標(biāo)準(zhǔn)化不明確四、 提高生產(chǎn)效率的十個(gè)關(guān)鍵技術(shù) 1. 人員效率大化2. 提高設(shè)備稼動(dòng)率3. 確保物料進(jìn)度4. 急單與插單應(yīng)對(duì)5.
張小強(qiáng)查看詳情
一、安全教育訓(xùn)練 1. 日常安全教育2. 新員工“三級(jí)”安全教育3. 特殊作業(yè)人員安全教育二、安全事故預(yù)防 1. 傷亡事故防范基本措施2. 安全意識(shí)強(qiáng)化3. 預(yù)知危險(xiǎn)訓(xùn)練4. 操作者人為失誤預(yù)防三、安全檢查 1. 安全檢查的內(nèi)容2. 安全檢查的方式3. 安全檢查的處理四、安全防護(hù)用品管理 1. 特殊勞動(dòng)防護(hù)用品規(guī)定2. 防護(hù)用品種類分析五、安全事故處理 1. 生產(chǎn)安全事故性質(zhì)2. 生產(chǎn)安全事故緊急處理3. 生產(chǎn)安全事故調(diào)查4. 生產(chǎn)安全事故分析六、現(xiàn)場(chǎng)安全排除技術(shù) 1. 險(xiǎn)情辨別2. 危害控制方法3. 移去 / 替代法4. 工程控制法5. 行政控制法6. PPE法7. 事故報(bào)告流程七、附<制造